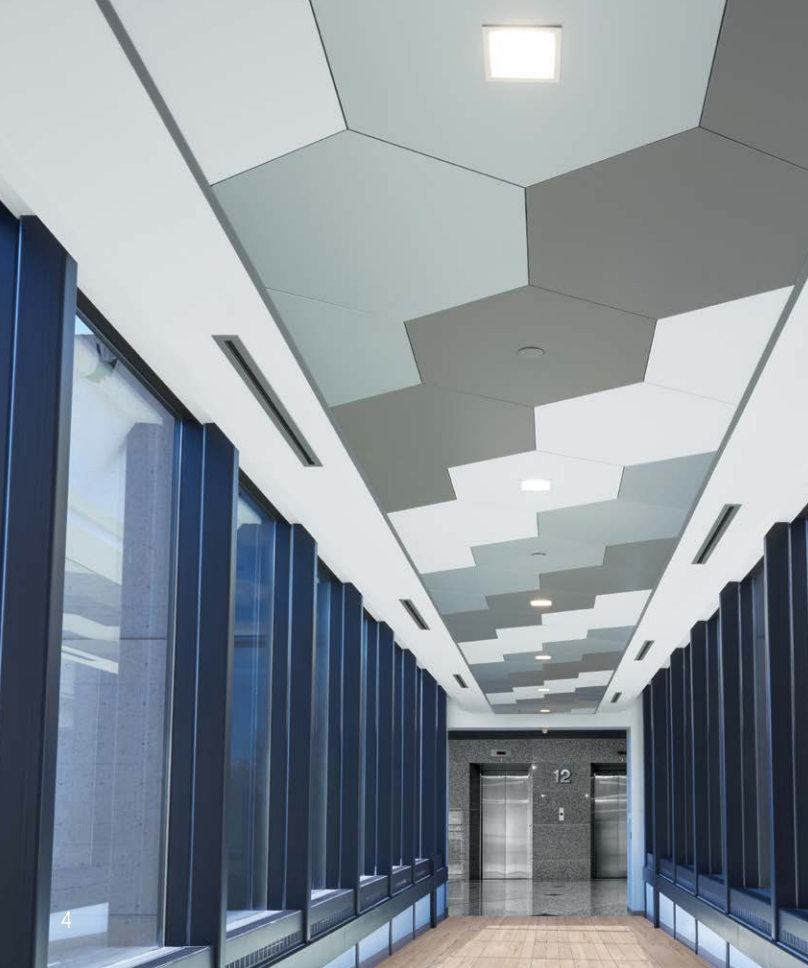
During this year’s Industrial Design Sprint Project, the program was proud to welcome Nick Friez (BsID ‘16) as one of our alumni guest critics. Nick is a product designer at Armstrong World Industries, a leader in the design and manufacture of ceiling, and wall solutions. Recently, he took some time to sit down with us and talk about some of the exciting things he’s doing at Armstrong:
So, what’s your position at Armstrong?
I’m a Staff Designer on the Product Design Team. We are responsible for creating new ceiling and wall products across a wide range of commercial applications from schools and hospitals to offices – Spaces that really benefit from improved acoustics and visual enhancement.
What’s the make-up of a team like that?
Our team is a mix of Industrial Designers, Engineers, CAD Specialists, and Installation Specialists, as well as a number of other cross functional members that collaborate together to bring new products to the market.
What’s working on the team like?
It is a really exciting and fast paced environment. We are designing a large number of projects simultaneously. The team that I’m on guides projects through the entire process from start to finish. That’s one of the things that I really like about my position. There aren’t separate teams handing portions of projects off to each other. All of our teams work together collaboratively. We see each design through until it’s in the product lineup and is ready to be specified and ordered by Architects and Contractors across the country.
Our design team is responsible for bringing in trend, material, and process information that is used to guide our design and development process. Starting with the research, concept, and ideation process, we review our ideas with Architect and design panels to gain valuable market and customer feedback. Then we do everything to move the project forward including the initial benchmarking and materials research. As we evolve the design, we make our own prototypes using laser cutters, CNC machines and 3D printers. Working through the manufacturing phase is a huge component as well. We even get to be part of the fire testing and seismic testing. Once a design is complete, we work with our marketing teams to get everything ready for a full product launch.
Is there a project that you’re especially proud of?
Recently I designed a product line called MetalWorks Torsion Spring Shapes. It’s a line of over 25 different geometric ceiling panel designs. I created a wide range of shapes and what’s great about each of them is that they’re both modular and dimensional. So when you put multiple pieces together you can make really distinctive designs that are specific to a space and create add a lot of interest and depth. It enables architects to add a whole different level of experience in a given environment. I had a lot of fun with that one.
What are some the things you’ve learned as you’ve developed at Armstrong?
I’ve learned new ways to work with the manufacturing side of things to quickly understand what’s possible and how it will affect the overall product’s form and function. I’ve also learned a lot about what it takes to bring a product to market. This includes putting together presentations and visuals in new ways that grab someone’s attention. There is a whole side to commercializing and marketing that is so important to the overall design process.
Looking back, what’s something from the Jefferson ID program that you’ve drawn on?
The realism. A very large portion of our design process at Armstrong is exactly what I learned during my time at Jefferson so the transition to the professional world was really straightforward for me. Even some of the 3D printers we use are the same 3D printers I worked with at Jefferson! Having such a strong foundation with the design process allowed me to focus more time on understanding the manufacturing, marketing, and commercialization side of new product development.
What advice do you have for developing industrial designers?
Being able to communicate your ideas through different methods and technologies is so important but never abandon the basics. Concept sketching to show someone your idea is always crucial. Not everyone has the design understanding that you have, so being able to quickly convey your ideas to others is huge. Basic perspective, proper line weight, all those small things will help someone who’s not a designer…get it.
What do you enjoy most about your work?
Having the ability to collaborate with so many other architects and designers. Being able to take those collaborative ideas and perspectives that start as just a conversation, and turn them into a product installed in an airport across the country a year later. There’s a tremendous satisfaction in that.
Add comment